Or how we experienced three summer vacations.
Click on illustration OR highlighted text to enlarge associated illustration for supporting information. |
Revision: 5-3-06
|
PREFACE
Click on the image blocks that don’t show to see the full image.
Overheating
Engine Temperature elevates to a point where normal engine operation is adversely affected (typically 215F to 220F) or the radiator expels fluid, about 230F or higher depending on the radiator cap pressure and altitude
Since our Tigers were produced in the mid-60’s, one of the things that has continued to be considered a problem has been the cooling system; in particular overheating after extended periods of idling on hot days. Some owners have been successful at cooling their Tigers and some are still trying to keep their Tigers cool. Solutions have been offered by others in the past, but have generally been based on empirical evidence, with no scientific testing or data to substantiate these solutions and conclusions.
This is the first fact and data based findings published regarding effective cooling solutions for the Tiger and some fan airflow information for Alpines. Our findings are also applicable and maybe of interest to other owners with similar engine cooling configurations with overheating problems.
Interstate Highway Testing
A prescribed route allowed constant 72MPH( 3,200 RPM) for approximately 12 minutes in each direction of the same rout. The vehicle traveled approximately one half hour or longer at similar speed before measurements were taken. Temperatures were considered stabilized with three consecutive measurements 2 minutes apart were repeatable with compensation for small ambient temperature changes.
This is the story of how this effort began, how it was done and facts you can use to keep your Tiger Kool.
This article is for typical street driving applications.
In the early summer of 2000 we decided to use Andy King’s (Chuck’s son) ‘66 Tiger as a test car. It had a recently rebuilt stock 260 two barrel engine with a stock radiator, fan and water pump. The engine had been “cooked out” prior to rebuilding, so we could be sure of good water flow through it. The stock radiator had been cleaned and rodded out and all hoses were new. At the beginning of this test the car would overheat at idle on hot days over 85F within ½ hour. (see box above) Keep in mind throughout this article that our testing was to correct overheating at an idle (see box below); but we also did tests at highway speeds (see box at left) to note the effects (positive or negative) of any changes we were making.
Idle Testing
Before each test, the test car was “heat soaked? by driving over a prescribed course for about 20 minutes. It was then parked in an area free of extraneous drafts and allowed to idle for the duration of the test at 850 to 900 RPM. Temperatures were considered stabilized when three consecutive measurements 2 minutes apart were repeatable.
We hoped to solve the overheating problem (at idle) by approaching it scientifically and documenting data to show changes in engine temperature resulting from controlled single-variable changes in the cooling system. We decided at the onset to use a calibrated digital temperature gauge so that we could accurately record small differences in engine temperature. We took temperature readings from the engine intake manifold temperature sensor port; also the inlet and outlet sides of the radiator to see what effect temperature differential, caused by different setups, had on engine temperature. We took ambient temperature measurements from a probe extending 18” in front of the grille area to an on board digital thermometer. This provided the most accurate method of measuring actual ambient air temperature entering the radiator. Temperature measurements were taken at two minute intervals which were plotted later as Time versus Temperature graphs to analyze results.
We began by testing five different radiators, including two popular aluminum radiators; two popular high volume water pumps along with stock pumps; and three different popular engine fans. None of these initial changes produced asignificant cooling improvement at idle [fig32]. We were however, able to see good improvement with some radiators at highway speeds [fig. 33] The effects were so dramatic that we had to weld the thermostat open (restrictor plate) [fig. 39]in order to record temp differences below the 180 degree thermostat used for testing.
This pointed to the real problem and the solution. Since we knew that at an idle the same setup wasn’t effective, what was the difference?
Airflow — put lots of air to the system and it works well. An engine and cooling system don’s know if the car is standing still or moving. We tested the hypothesis that airflow would give the improvements we were looking for by simply trying a 10” electric pusher fan at an idle, in conjunction with the mechanical fan we were testing at that point and seeing the outcome [fig. 34]. We went from having to shut the car off due to overheating to having the car run at an acceptable stable temperature for over an hour and shutting it off at our discretion.
So we started to concentrate on ways to get more air. We needed to be able to quantify the amount of airflow a given mechanical or electric fan or shroud change would produce before testing each item in the car. We wanted to test each item in an identical fashion so we developed our “air-buck” [fig. 23]. We took the front clip from an Alpine and enclosed it in plastic except for around the grille. We cut the plastic over the hood area and sealed it with velcro for quick opening and closing for easy access to make our single variable airflow design experiments.
An exhaust port tube [fig. 24] in the rear allowed us to quantify the air exiting using an anemometer. An electric motor fitted with a digital tachometer and variable speed control was used to drive the mechanical fans. The motor had a fan/pulley hub on its shaft and was aligned to the radiator the same as in the actual car, but on a movable mount to allow us to change the fan to radiator distance.
Although time consuming to make up, we could quickly do repeatable quantitative tests at a set idle speed rather than just taking what may have been a good choice and testing it in the car — a five minute test as opposed to one that took three hours. We then had quantitative data rather than end result data based on gut feelings. The best airflow data on variables was the criteria used for in-car testing. Since we knew it was improved airflow we were looking for, we could quickly rule out fans or set-ups that weren’t in contention.
We even made a second air-buck made of a wooden frame enclosed in plastic [fig. 45] with similar volume to the first with no grille area, only the radiator opening. This way we could do test comparisons between the two bucks to be sure there was nothing about the grille design that would encumber air flow. The test between the air-bucks showed no difference at idle.
Our air-buck allowed us to test engine driven and electric fans, shrouds, relationships of fans to shrouds and fan to radiator distance [fig. 25]. Even increasing fan RPM [fig. 37] was a simple way to increase airflow. For example Chuck found a water pump pulley that was 12% smaller diameter than stock that gives a corresponding 12% increase in fan speed. It is from a 1978 to 1982 six-cylinder Ford Fairmont/Mercury Zephyr. It has the same bolt hole pattern as a standard Ford water pump hub (Center hole needs enlarged to 1” if you are using an original Tiger water pump fan hub).
After evaluating and determining the best engine driven fans [fig. 10], fan shroud design [fig. 11], engine fan / radiator spacing [fig. 12] and other air flow enhancements, we then tested pusher electric fans. We couldn’t rely on manufacturers’ propaganda because of rating differences between manufactures. Again, we used our “air-buck” to test the fans. We tested a variety of junkyard as well as store-bought electric fans [fig. 10]. We had good results with 10”, 11” and 11 1/2 “ electric fans. Generally, the simple large paddle type 4 to 7 bladed fans [fig. 6] pushed more air and were the quietest. The fancy high [fig. 5] blade count turbine [fig. 5] looking aftermarket fans were the poor performers [fig. 4] and typically produced an annoying high pitched sound. Surprisingly, with all electric fans, keeping the housing of the fan about an inch away from the radiator gave considerably better results than when it was pressed tight against it.
In a nutshell, things that gave improved airflow were
Aftermarket 15” fans that provided the most airflow were:
Note: Larger diameter 15” engine fans may require raising the engine slightly to accommodate. (1/8th” thick washer at each engine mount raises the fan tips approximately 1/4” at the rack.) A common error is to cut the fan’s diameter to 14” to fit the car, DO NOT DO IT or SIGNIFICANT AIR FLOW will be lost [fig.10]
- Shroud VS no shroud [fig. 11]
- A completely enclosed shroud [fig. 28] with a sealed perimeter
- Fan position and clearance: Leading edge of the fan blades 1” to 1 1/8th” from the radiator, Fan tips 3/4” from the inside edge of the shroud; fan blades 1/2 to 2/3 out of the shroud.
- Increase engine idle RPM to at least 900 RPM during hot weather
- Use of a smaller diameter water pump pulley
- Use of an auxiliary electric fan
We were also interested in where the air is coming from that feeds through the radiator. By using mylar strips cut from a cassette tape and placing them in different openings in the grill/radiator area, we could observe any air movement and its direction. This made it possible for us to see hot air from the engine compartment being recirculated through the front of the radiator, which is the same as adding higher ambient air temperature.
Blocking the horn holes [fig. 38] has for years been one of the things known empirically to have been helpful in reducing engine temperature, both at an idle and on the highway. This is for two different reasons. At highway speeds, a significant amount of air is wasted entering the engine compartment instead of passing through the radiator when the horn holes are open. With horn holes closed the maximum amount of airflow passes through the radiator. At an idle, the positive pressure from inside the engine compartment (caused by the fan) forces hot air in the engine compartment out the horn holes, which is then recirculated through the radiator, causing heat to accumulate.
A similar problem at idle is that the positive pressure in the engine compartment forces hot air out between the crossmember and the bottom of the radiator. Because of the negative pressure in front of the radiator, this hot air is recirculated through the radiator once again causing heat to accumulate. So blocking this opening (with foam and/or with a fabricated air dam) also helps to improve idle cooling [fig. 15].
Water flow is an issue in itself. This includes thermostats, restrictor plates, water pumps, redistribution of engine and pump water flow. Our test comparison with and without a thermostat or a restrictor plate indicated a significant cooling improvement at idle when using a thermostat. This indicated a slower, more restricted flow of water was helpful. Some of you may not think that’s logical, but you have to accept the data [fig. 16].
To further confirm this, high volume water pumps had a detrimental effect at idle in our test car. This may not be the case in larger capacity radiators or systems. This had been an issue of contention among some owners with us based on our initial testing in 2000 and 2001 [fig. 46].
For this reason additional testing was repeated and refined in 2003. There are two different versions of the stock water pumps [fig. 41]; one has vaned impellors, the other has paddles. We decided to compare each of these against one and the other as well as the Milodon high volume [fig. 42] water pump. We recorded both idle and highway data in 2003. During 2000 and 2001 high volume water pump idle tests results were so poor that we did not test them on the highway.
During all these water pump tests a restrictor plate was used in order to measure temperature differences that would have been below the thermostat temperature. We found that at an idle these results demonstrated the same improvement with stock pumps as tests two years earlier. Test results indicate that stock water pumps significantly outperform the high volume pump at idle. Interestingly during highway testing the high volume pump slightly outperformed the stock pumps, but all pumps produced engine temperatures well below thermostat temperatures at highway speeds. For this reason a high volume water pump for normal highway use has little value. On the other hand, with a significant decrease of temperature observed at idle, we feel using a stock vaned pump is the most advantageous [fig. 35].
Additionally, on the issue of water flow, we changed the distribution of water from the engine to the radiator in three different configurations. The first eliminated the bypass hose from the thermostat housing to the water pump by squeezing the hose shut. The bypass hose assures water circulates through the engine at all times regardless of thermostat opening. It is 1/4 the diameter of the upper radiator hose leaving the intake. That’s a considerable amount of circulating water that never goes through the radiator when the bypass is functional. So, blocking the bypass should allow more water to pass through to the radiator. Well, this increased engine temperature at an idle [fig. 36].
We then tried a second rerouting method. We ran a hose from the bypass connection outlet of the thermostat housing into the lower inlet hose to the radiator from the overflow reservoir (header tank) and blocked off the bypass at the water pump. We felt possibly since the upper (inlet) hose to the radiator is smaller than the lower (outlet) hose, the upper hose could somehow restrict the extra volume of water. This still raised the engine temperature exactly the same amount as when we simply blocked the bypass. The third and last approach was adding a bypass shunt by routing a hose the size of the bypass hose from the lower radiator hose to the bypass connection on the water pump with the intake manifold side of the bypass routed through the reservoir inlet to the radiator. This test method was tried in case it had something to do with water pressure or volume at the pump into the engine. Still exactly the same rise in engine temp as when the bypass was blocked.
It seems safe to say increasing water flow/volume or distribution to the radiator does not help idle cooling in our cars, at least within the parameters we described.
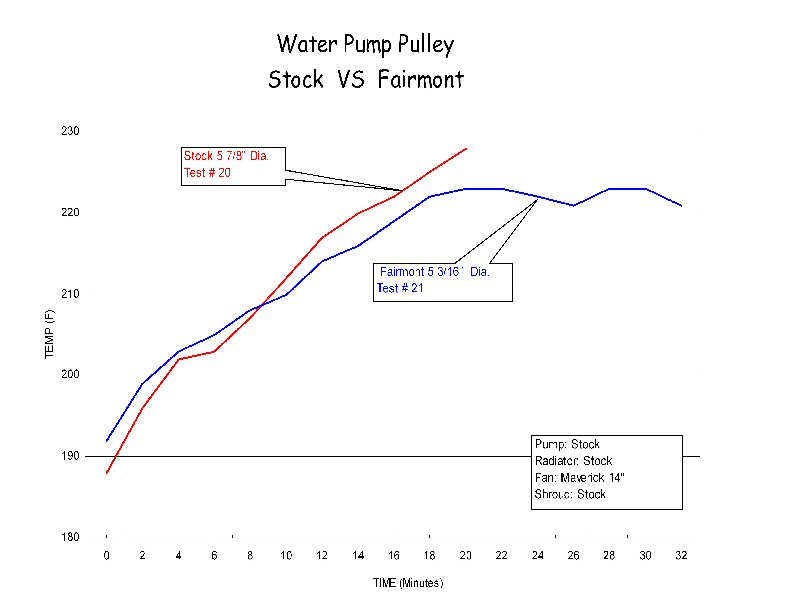
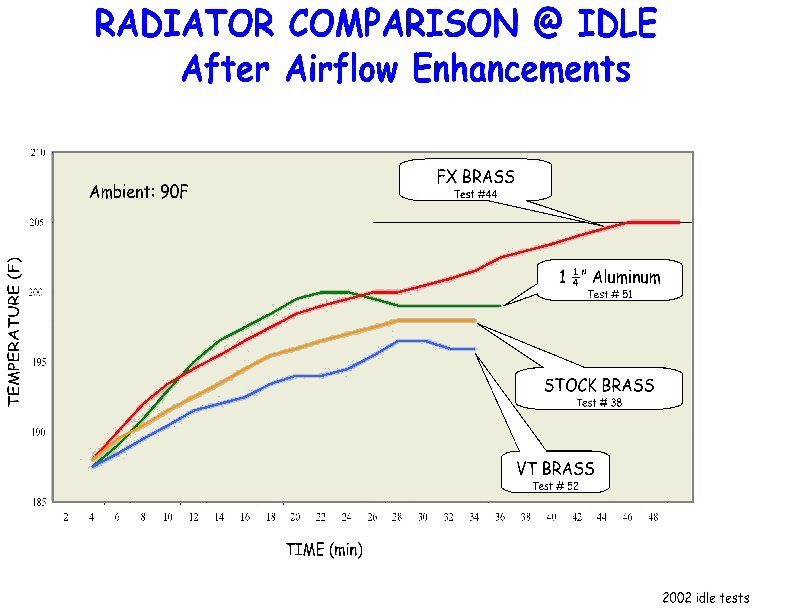
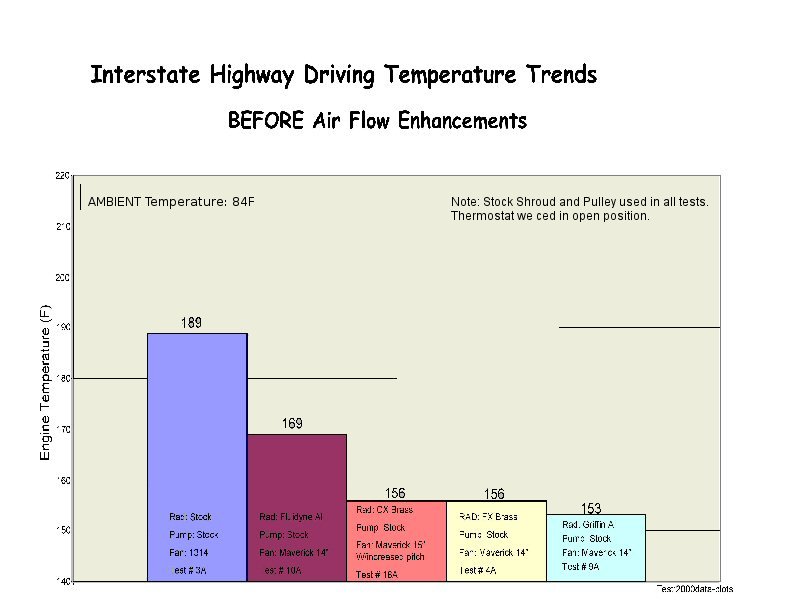
The one place that engine temperature did not rise with increased water flow was when it happened in tandem with increasing air flow by using the smaller water pump pulley from the Fairmont. This 12% smaller pulley increased the mechanical fan speed and water pump speed by 12%. This decreased engine temperature [fig. 14] significantly. We feel the beneficial effect of increased fan speed and resulting airflow outweighs the detrimental effect of the increased water flow caused by the smaller diameter pulley.
After gaining all we could with increasing airflow, we went back to test a variety of radiators, some that we had purchased or already had, and ones that were generously loaned to us for testing from others. Surprisingly, even though we found differences among them, some were a little better at an idle than stock [fig. 27], and some a little worse. Most of them were better than stock on the highway [fig. 33], but even there, the stock was acceptable. Although the results were not necessarily what we expected, it emphasized the real importance, once again, of maximizing airflow and the value of scientific testing over anecdotal conclusions.
Remember, one of the reasons we did highway tests was to be sure that changes we made for improving idling would have no detrimental effects at highway speeds. So the next tests did not have to do with idle temperatures, but since we were set up to test them and they were simple enough to do, we did them. We found that placing an electric fan (especially the larger ones) in front of the radiator raised engine temperature at highway speeds [fig. 18] by several degrees. We then tested changes in engine temperature at highway speeds that were made by removing the brace [fig. 18] at the bottom of the radiator. This brace blocks at least the bottom three rows of tubes in the radiator (approximately 10%).
Removing this brace decreased engine temperature by 2 to 4 degrees. We also did tests on the use of an air dam [fig. 19] in front of and 2” below the cross member at highway speeds. The air dam decreased engine temperature by 2 to 3 degrees as well. This also had the added benefit of replacing the brace at the bottom of the radiator without covering any of the tubes. Short air directors (ones that did not go below crossmember and were within the valance) actually increased engine temperature slightly on the highway.
What’s of importance here is that any undesirable effect that the electric fan had at highway speeds was compensated for by removing the brace [fig. 3] and using an air dam. This may not be of great significance because most of the highway tests with improved radiators were well under thermostat temperatures (180°), even on 100 F days. The testing became so involved and time consuming that it took us three + summers to run our tests and ultimately verify them. The summer of 2002 was perfect for our testing, with many days in the 90°’s and even 100°+ days, with no rain — bad for the farmers, but good for us. We were not only able to do new tests, but also were able to verify our old tests, even under more stressful conditions. Original tests (2000-2001) without our improvements were virtually identical to those same tests repeated in 2002.
Conversely, with all our improvements in place we were able to let the car idle for well over an hour at under 210° even on 100°+ F days without an assist from an electric fan. We achieved our goal!!!!! With the electric fan turned on, obviously engine temperatures would be brought down even further [fig. 4].
Notes of interest
Having the electric fan on a variable-temp thermostatically controlled switch (set at approximately 195°) wired and fused to the constant hot side of the fuse block is a good idea as you can almost certainly count on the fan shutting off when the car is moving over 35 MPH. When the car is shut down on a hot day, the radiator and engine compartment temperature will continue to rise, fuel lines may vaporlock, the carburetor fuel may percolate (boil) and the car may be difficult if not impossible to start. Allowing the electric fan to come on with the engine off reduces this problem.
Besides the electric fan testing, as an assist to idle cooling, we also cut openings into the upper part of the inner fenderwells behind where the voltage regulator and servo are mounted. The opening was about the same size and location used for the Tiger LAT 41 side vents. In theory this provides an exit for hot air pushed by the fan(s) at an idle, also when the engine is shut off but still building heat. We made some evaluations of these vents open and closed before and after airflow enhancements were incorporated. We only detected about a two degree improvement with these open during idle [fig. 21]. Since most Alpines and Tigers do not have these openings and it is difficult to make this change neatly we elected not to recommend this change.
The popular Griffin aluminum radiator was one of the better performers on the highway and performed well at idle, but only with the airflow improvements [fig. 27]. An extremely important point about this radiator was, until airflow increased to a certain level, it was one of the poorer performers at an idle (it was always great on the highway). The copper/brass radiators were more responsive at lower airflow rates. So if you have an aluminum radiator without maximizing airflow at an idle, you may not be doing yourself a favor.
Some other observations while doing these tests validate horror stories with engine fans. That is, fan blade separation and launching through hoods. In several of our experiments we noticed fan blades and water pump hubs with stress cracks ([fig. 29] 1 & 2 [fig. 13]) that were leading to eventual separation. The most serious problem is the 4-bladed stamped steel fans [fig. 9] used on the four cylinder Sunbeams from 1964 and later. The blade pitch cannot be safely altered on these blades. Pre-1964 four cylinder six bladed fans with riveted blades can have the pitch modified [fig. 8].
The Ford Maverick C9DZ-8600 pitch can be altered [fig. 7] without introducing stress cracks. Increasing the pitch significantly improves airflow [fig. 10]. Several of the stock Tiger water pump pulleys had stress cracks emanating from the mounting holes [fig. 13]. The Fairmont pulley design resolves this design weakness because of its
increased thickness [fig. 40].
A popular anecdote or magic elixir has been to add products to the water like water wetters to make the car run cooler. Our tests indicate insignificant improvement at idle [fig. 20]. Sometimes a suggested fix is the use of the heater core as an emergency cooling device. Our tests indicated less than 2 degree improvement [fig. 17] at idle. Although not shown, we did not experience any appreciable cooling benefits at highway speeds.
Believe us when we say “airflow is the cure“; It’s notably the least expensive thing you could ask for, and it works! For example, the simple change to a large higher pitch fan and the use of a smaller diameter water pump pulley provides major cooling improvements.
We learned a lot throughout our tests and found a definite learning curve for doing the testing itself, but we feel we’ve not only solved the Tiger’s cooling problem, but can back up our recommendations with sufficient data of our results to substantiate them. A note of interest regarding our testing is that our recommended cooling enhancements are applicable in concept to other similar applications as the Tiger. Examples include V8, V6 and 4cyl cars like Alpines, MG, Triumph, Austin Healey, Griffith, Daimler SP250, Warwick GT, etc. Review the following summary of our best cooling enhancements determined through our testing.
Summary of best cooling enhancements
(Experienced in these tests)
The combination of enhancements is required to maximize cooling. No one change is the cure.
AIR FLOW ENHANCEMENTS:
- Block horn holes
- Block gap between crossmember and bottom of radiator
- Remove brace in front of lower part of radiator.
- Air dam directly in front of crossmember and 2” below.
- Fan shroud, stock
Enclose and seal fan shroud (metal on bottom of shroud completely encompasses blades)
Fan blades:
- Tips 3/4” from shroud edge.
- 1/2 to 2/3 outside of shroud.
- Leading edge to radiator clearance, 1” to1-1/8” @ 3 and 9 o’clock position (As required; Bend/trim shroud; move engine; reposition water pump pulley; shim fan. Derale fan design helps establish desired position.)
ENGINE DRIVEN FAN: 15”
Imperial #221615 (Increase pitch on blades symmetrically to within 1/4” to 1/2” of fan belt.
NOTE: Fans may require:
- Careful repositioning of upper radiator hose. [Use Gates hose #20704 (or equiv). Cut off radiator and T-housing ends to allow fan blade clearance. (May 2020)]
- Use of stock length thermostat housing.
- Raising engine so fan clears rack by adding washers between engine and mount.
NEVER, NEVER, NEVER reduce fan diameter to make fan fit.
ELECTRIC FANS:
- Pusher type, 10” to 11” (Mount 1” away from radiator)
- Use fans with 4 to 7 paddle type blades, not the popular narrow turbine like blades which are noisier and less efficient. Fans larger than 11” dia. have a detrimental effect at highway speeds. Connect to a thermostatically controlled switch.
WATER PUMP:
Stock Vane type
RADIATORS:
Virtually all radiators performed well in these tests when airflow enhancements were incorporated.
Two good choices beside stock;
- Three row brass VT Windsor core #128366 by Go/Dan industries. Use to recore existing radiator.
- Griffin 1¼” or 1½” Aluminum for complete bolt in radiator.
WATER PUMP PULLEY:
78-’82 6 cyl Ford Fairmont & Mercury Zephyr, 5 3/16” diameter. 2 or 3 groove OK.
THERMOSTAT:
Use at least 180F degree.
EPILOGUE
Hopefully, you’ll take this information as credible and find the progression of our tests as interesting as we did. A lot of time, effort and money went into our testing. It is important to remember that, this exercise would not have been possible without the encouragement and contributions of many owners. We should all be indebted to the individuals listed below who generously contributed items like, fans, radiators and pumps and even cars, as well as ideas and general support. In addition, we are deeply indebted to Cpl. Andy King, USMC, for his testing assistance and use of his Tiger for idle and highway testing that approached a thousand hours.
Chuck King & Tiger Tom
Contributors
(Listed alphabetically)
Dale Akuszewski (Dales Restorations), CA
Larry Bailor, PA
Tom Ballou, TX
Gary Carlson (Middletown Radiator), PA
Donna D’Amelio (Website host), VA
John Engle, OH
Ed Esslinger, AL
Rick Flynn, UK
Tom Hall, CA
Doug Jennings (Tiger Auto), OH
Wanda King, PA
Ron Kirk, TN
Steve Lafiman, CA
Gary Latshaw, PA
John Logan MI,
Rick McCurdy Jr., NY
Rick Mcleod (Sunbeam Specialties), CA
Larry Paulick, MD
Paul Reisentz, (Reisentz Restorations) CA
Doug Stockman, OH
Buck Trippel, CA
Henry Vicioso, IL